Background
In recent years, China has attached great importance to the development of the intelligent manufacturing industry. Policies and measures have been introduced to provide continuous policy support for capital, technology, and support platform, and to promote the integrated development of new-generation information technology and the manufacturing industry.
Take a smart factory as an example. As a key industry in digital transformation and a key industry in 5G application cultivation, the smart factory is undoubtedly the general trend of modern industry and manufacturing industry, and a fast and optimized path to realizing enterprise transformation and upgrading.
According to statistics, the market size of China's smart factory in 2020 is 856 billion yuan. According to the enthusiasm and expansion speed of smart factory construction in various industries, it is expected that China's smart factory industry will maintain an average annual growth rate of more than 10% in the next few years, and the market size of China's smart factory industry is expected to exceed 1.4 trillion yuan by 2025. There is no doubt that the 5G+ "smart factory" is a new form of manufacturing and a new engine for future manufacturing.
Pain Point
The workshop area is large, the storage location is scattered, the wireless network covers many dead spots, the network disconnection occurs frequently, and the on-site situation cannot be controlled in real time.
Traditional factory operation mode is backward, needs to consume a long production cycle, the production cost of enterprises is too high, and the production efficiency cannot be effectively guaranteed.
Factory internal equipment automation degree is low, need to rely on manual handling, labor intensity, safety, and labor cost problems are difficult to be solved.
The factory warehouse environment is complex, with a mixed flow of people and vehicles and frequent vehicle movement. The existing manual management mode is backward, with low efficiency and high error rate, and problems cannot be dealt with in time.
IoT Factory Data Acquisition and Monitoring Solution Introduction
To solve the problems of traditional factories, such as "difficult labor, high cost and long cycle", Four-Faith uses the features of 5G, such as wide coverage, large connection, low delay, and high reliability, to build digital workshops and intelligent factories, to realize the transparency of production and operation of smart factories and efficient collaborative manufacturing of remote factories.
The data acquisition and monitoring scheme of Four-Faith 5G+ smart factory fully considers the difficulty of site wiring and the current situation of intensive installation of the machine. By adding 5.8G Wi-Fi wireless network card, the machine connects with Four-Faith 5G industrial router through Wi-Fi function and uses 5G industrial router to install 5G special network card to combine with telecom 5G base station network. The network is interconnected with the back-end server group, and the private network is isolated from the public network, effectively ensuring the security of manufacturing data.
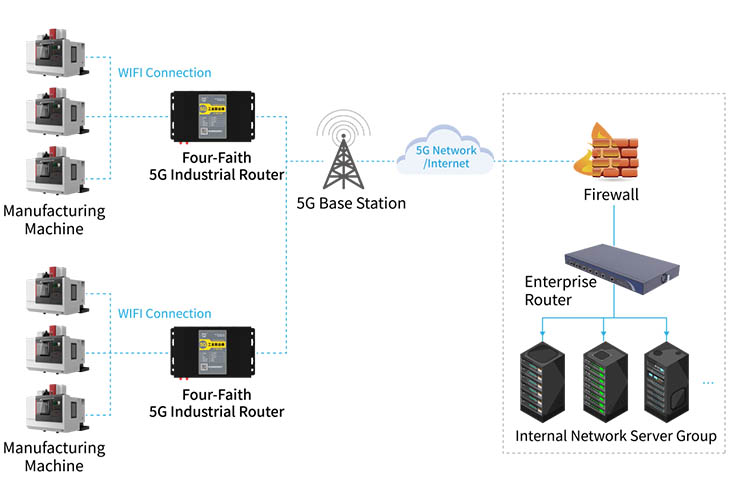
At the same time, through the effective installation and layout of 5G industrial routers, the function of wireless networking of machines in the WiFi coverage area is realized, and the function of low time extension and large bandwidth of 5G network can also effectively guarantee the real-time performance of data so that the back-end service can monitor the current production situation and machine parameter information in real-time to ensure that data is not lost.
Digital Factory Data Acquisition and Monitoring Solution Advantages:
1. Datamation
Digital factory data acquisition and monitoring solution using Internet technology to achieve efficient information interconnection between equipment, digital factory "couplet factory" to upgrade, the operator can realize collection production equipment, material, finished products, such as dynamic production data, timely grasp the production operation, realize the seamless docking of the production environment and information system, enhance the awareness and monitoring ability, meet the demand of IoT factory 24 hours monitoring.
2. Integration
Building enterprise information integration platform, realizing the seamless connection of upstream and downstream data, supporting enterprise operation and management upward, and highly integrating with real-time data of production process downward, forming a complete and reliable production chain, making plans available and controllable, plan execution transparent, production cycle controllable, and improving the utilization rate of equipment resources.
3. Visualization
Real-time control of equipment production process to ensure stable and controllable product quality. At the same time, the data screen can be realized, and the abnormal problems can be timely warned. The administrator can find the problems the first time, adjust the production plan in time, and improve the enterprise operation and management decisions.
4. Traceability
IoT factory data acquisition and monitoring solution perfectly solves the problem that workshop production quality cannot be effectively managed, and data information cannot be traced and realizes real-time monitoring and control of production process, traceability of production information, and scientific operation and maintenance of digital workshop.
5. Real Time
With the characteristics of large bandwidth and low delay of 5G network, the delay between the terminal and the back-end server can be controlled at about 10ms to ensure real-time data to the greatest extent. Meanwhile, large bandwidth can also meet the requirements of industrial scenarios.
6. Wiring Free
From "Digital Factory" to "IoT Factory", data acquisition and monitoring solution of 5G+ smart factory provides powerful dual-frequency WiFi access capability. For fixed or mobile production devices, wireless networking can be realized through WiFi access to avoid wiring installation problems.